The first in our Guest Blogger Series comes from Brett Taylor, Director of Bornhorst + Ward.Brett has been the Director in charge of Bornhorst & Ward’s successful implementation of Revit. With 8 years of personal hands on use of Revit he has a vast level of experience to share. Bornhorst & Ward have fully documented 100% of their projects using Revit since the start of 2007.
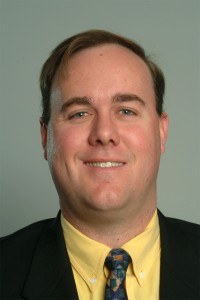
He has worked on many projects where Revit has been utilised in an integrated approach to design modelling. These projects include The Village at Coorparoo, Regent Office Building, G40 Griffith Health Centre & Ergon Office Building Townsville. He has spent many hours collaborating with clients, fellow consultants, contractors and sub-contractors to develop the BIM workflow, integrated modelling approach that has enabled the successful delivery of many projects…
20% Saving in Building Costs:
For the last 8 years the team at Bornhorst & Ward have been working in the Virtual Design World to improve our work processes utilising 3D models to change how we go about delivering our civil and structural engineering services.
Since the start of 2007 we have fully documented all of our structural projects in 3D using Autodesk’s Revit software. We also link our Revit models to our design software programs. So where it took 2 weeks to create an analysis model we can obtain accurate building deflections, refer figure1, and load rundowns in a fraction of the time. This process has helped obtain more accurate structural sizing earlier in a project and enabled us to look at engineered options to develop the best solution for projects. Which helps reduce risk on the project!
Figure 1 – Deflection Plot of a typical Residential Project
The key to Virtual Modelling is to store information in the model which can be accessed by project team members to avoid duplication of information and elements within the model. We have been storing information in our models that has been used by our co-consultants. Information like concrete strengths, reinforcement rates, steel finishes & QSID. This has enabled our co-consultants like Quantity Surveyors and Steel Detailers to use our models and the information contained in them to speed up the workflow, improve accuracy and save building costs.
A good example is the steel shop detailing process. It is still common today that the following process occurs:-
Current projects go from a 3D engineering model to 2D drawings (produced by the design consultant), then a new 3D model is created to then create 2D shop drawings (by the steel detailer). The Building is then constructed. How smart is that!
The technology is currently available where 3D models can be transferred and utilised by all parties, including the fabricator in the steel factory and the builder on site. Which means 2D drawings are not necessarily required. That way anyone who views the 3D model can see the whole building, not just what is shown on the plans or sections which have been created.
We have been working with Phil Shanks at Jackson Roxborough Steel Detailers for a number of years to refine the workflow of transferring the 3D models between our offices and between the software that we both use. We can now overlay models to find any differences between the two models and the information contained in the models.
A good example of this is shown in Figure 2 below
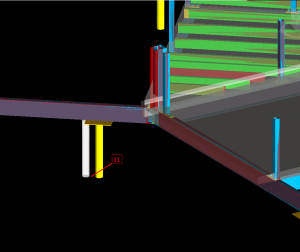
Figure 2
The yellow screw pile in the shop detailer’s model doesn’t line up with the white screw pile that was in the engineering model. A late change to the pile location was required and made to the engineering model after the model was exchanged. This was quickly picked up when the models were checked. There was a fair chance that if 2D shop models were reviewed this issue would not have been identified and the steelwork would have needed adjusting on site causing cost and time issues.
The above examples are just small structural engineering stories from the whole building workflow but they a replicated throughout offices of companies which embraced change and are working in the Virtual Design environment. It is not a quick process to change workflows but it worth the effort as the time and cost benefits to our company, people we work with and our projects have been enormous.
Not only have we identified substantial time & cost benefits. Our project partners including the ultimate project cost have achieved time & cost savings.
I sat in a meeting recently where the UK government’s strategy for BIM implementation was explained. They had some simple objectives and requirements, a couple being
- All government projects delivered in a 3D collaborative environment by 2016
- 20% capital cost reduction for the construction phase.
On a recent pilot project they advised that the 20% capital cost reduction was nearly achieved. This then drove a change in the objective where they are now aiming for 33% cost saving in the construction costs of a project by 2025.
So where do we sit here in Australia? Well our government recently declined a request from the Building Smart organisation for funding to develop Australian Standards in BIM adoption and implementation. So it looks like it won’t just be Cricket & Rugby where the Poms are going to smash us!
It appears our government isn’t going to provide leadership. Therefore private enterprise will need to keep punching above our weight to achieve the efficiencies our construction industry needs to stay competitive globally.
There are many organisations who are extremely competent in the Virtual Design world and are providing benefits to the construction industry. If you are being told that BIM and Virtual Modelling is going to cost you more money and take longer then you are taking advice from inexperienced operators. If you aren’t walking through your proposed building using your ipad or computer you haven’t got the right design team on your project. If your builder isn’t showing you how they are going to construct your building and manage the subcontractors using a virtual building model you have the wrong builder!
If your company wishes to discuss this further and to find out how you can achieve the 20% saving that the Poms have achieved on your next Building Project please contact Brett Taylor at Bornhorst & Ward b.taylor@bornhorstward.com.au